Saniflo Provides Efficient Plumbing Solution
Although Loggerhead Inn and Suites emanates historic charm, the hotel recently needed renovations to accommodate all different types of travelers and price points. Once the renovation to all 29 rooms was completed, problems with the existing, aging cast iron plumbing-drainage infrastructure started to arise.
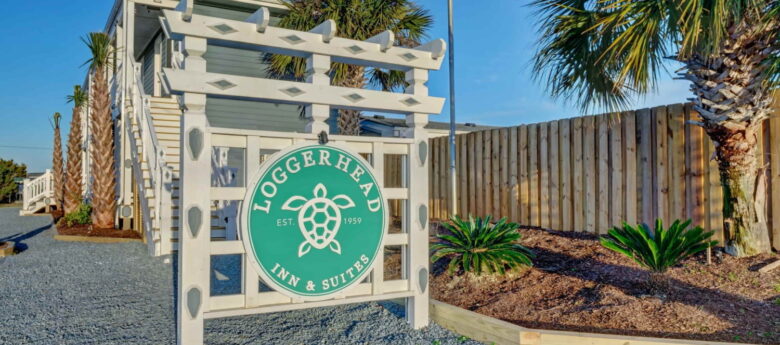
Nestled just a few steps away from the Atlantic coast, Loggerhead Inn and Suites provides the comforts of home in a quintessential beach town to visitors from across the country. Situated on Topsail Island, Loggerhead Inn and Suites is one of the island’s first family-owned motor inns and has hosted guests since the 1950s. The hotel’s prime location is one of the many highlights that puts guest vacation needs right at their fingertips.
Although Loggerhead Inn and Suites emanates historic charm, the hotel recently needed renovations to accommodate all different types of travelers and price points. The hotel’s front building was gutted from the slab up and rebuilt in its entirety, while the other four buildings underwent a complete rehab.
Once the renovation to all 29 rooms was completed, problems with the existing, aging cast iron plumbing-drainage infrastructure started to arise. Although the extensive rebuild and renovation brought the building up to code, an inspection of the plumbing lines was not conducted, leading to a complicated scenario.
When Brandy Owens, former Loggerhead Operations manager, stepped into the role in January 2021, the management company was unaware of the poor condition of the plumbing. “We did not anticipate this scenario after the renovations,” explains Owens. “We were consistently having to jet the lines, but with no improvement.”
That’s when Owens reached out to James Capp of Capp Plumbing, a family-owned business in the Surf City area.
According to Capp, despite the comprehensive, slab-up renovations, the plumbing underneath began experiencing “numerous problems, with everything backing up,” says Capp. Guests were reporting clogging and overflowing toilets in multiple bathrooms. Due to the inconvenience, the hotel lost revenue because of refunds to understandably upset customers.
After cleaning and jetting the pipes three times and investigating further with a camera, Capp found that the cast iron was corroded and brittle, leaving only limited options for repairing the existing plumbing. Some of those options came with a high price tag.
“One option was to tear down the building and install brand-new plumbing,” says Capp. “A second was for another company to reline all the cast iron pipes. But there was no guarantee on a job that could cost upwards of $100,000,” he explains.
Of course, Loggerhead management wanted to avoid these unrealistically expensive alternatives. They were desperate to find an innovative plumbing solution that could avoid costly alternatives while also minimizing downtime.
As luck would have it, Capps had experience with a more cost-efficient and reliable plumbing solution: Saniflo’s above-floor plumbing systems. After reaching out to Saniflo headquarters in Edison, New Jersey, he learned that the company offered a grinder system with a built-in grinder blade that was ideal for heavier-duty commercial applications – the Sanibest Pro.
The Sanibest Pro is used to install a complete bathroom up to 25 feet below the sewer line or up to 150-feet away from the soil stack. This one-horsepower pump system contains three inlets to handle drainage for a full bathroom. Aside from the 4-inch inlet for toilet connection, a 2-inch inlet on either side of the unit easily connects to other sanitary fixtures – a sink, a bathtub or a shower – to drain gray water.
The top of the unit houses a 1.5-inch vent port and .75-inch discharge connection. A service panel on top of the pump allows for easy access to all components inside.
The grinder pump connects to a toilet equipped with a horizontal rear discharge spigot, and the toilet tank connects to the water supply. The pump connects to the small-diameter discharge pipework, the sewer vent, and the electrical supply.
With the Saniflo solution in hand, Capp and his team of five plumbers went to work. After removing the existing toilets, they installed a Sanibest Pro in each of eight different bathrooms, running the discharge line vertically to the main plumbing drainage line in the attic; and the vent stack through the roof.
Here’s how Loggerhead’s plumbing is set up:
- A one-inch discharge pipe connects to each Sanibest Pro unit and runs a total of 15-feet – 8-feet vertically and 7-feet horizontally – before connecting to another discharge pipe feeding into the attic line.
- In one building, six guest-room units tie into a 3-inch discharge pipe.
- In the second building, two additional units tie into a 4-inch line.
Finally, the main PVC drainage line in the attic runs, via gravity, approximately 100 feet into the main municipal sewer access, located in the middle of the alleyway.
Loggerhead Inn and Suites was up and running again with eight new systems installed within two weeks. In the hospitality industry, it’s of the utmost importance to minimize downtime in maintenance and repair situations, of course. With zero issues reported since installing the eight Sanibest Pro units, the hotel is successfully operating without a hitch.
“I have installed Saniflo products in the past,” says Capps, “so I was confident that this was the best solution for the hotel to address their plumbing issues, but without the hefty price tag and a lengthy downtime.”
Former Operations manager Owens reports that the hotel began reaping the benefits immediately after installation. Multiple service calls can become a major headache and expense: Since installing the eight Sanibest Pro units, the cost-savings are evident to a much happier management.
“We haven’t had anything backing up or any plumbing issues at all,” she explains. “It’s been amazing to have trust in the Saniflo units and not have additional costs that come with repairs.”
